Information Overview



-
Inclinometer (tilt sensor) is used to measure elevation tilt with respect to gravity. Most inclinometers use a MEMS sensor which has been proven to have an extremely high reliability.
-
For an azimuth tracker axis, a combination of a limit switch and motor encoder is used. At power-up, the tracker is moved up against the limit switch. A motor encoder delivers electrical pulses which is counted by the Encoder Counter module.

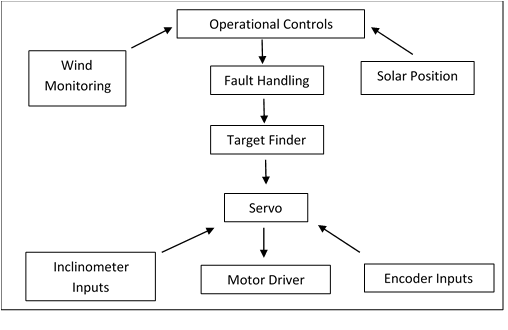
A state of the art solar tracker controller
incorporates a set of basic software modules for tracker operations. At the
executive level, the Operational module considers environmental conditions such
as wind, and current solar position to dispatch a tracker target command. The
Fault Handler module accepts the target and acts as the supervisor for the servo
module which task it is to move the tracker to its target.
Optical vs Calculated Positioning
There are two methods commonly used to control solar trackers: 1) optical sensing and 2) calculated sun position. Optical sensing mechanisms only work if the skies are clear, and do not perform well if the sensors become dirty. They commonly use analog electronic circuitry; hence they cannot be controlled remotely. Controllers based on a solar ephemeral equation typically calculate the solar position to 0.01 degree. During early morning and late afternoon, some solar beam deviation will exist due to the atmospheric water vapor deflection, amounting to as much as 1-2 degrees.
Feedback Methods
Solar tracker positional feedback is typically done through the use of encoders, limit switches, or inclinometers. Motor mounted encoders are typically most cost effective, but also introduce inaccuracies caused by the mechanical gears. For those systems, the gear slop can easily reach +/- 1 degree. Another variable is the tracker platform itself, such as bearings or the ductility of the construction materials. Long term failure rates for encoder-based systems can also be higher than expected due to fouling.
How Important is Accuracy?
In the case of using PV modules, the modules are not particularly sensitive with respect to the incoming solar beam. For instance, a solar tracker that is consistently off by 2.5 degrees is operating at 99.9% of its optimal output. Similarly, a tracker operating at 10 degrees deviation from the optimal solar beam will operate at 98.5% of the optimal output. Thus, it should be apparent that constructing a PV solar tracker with emphasis on accuracy may yield a poor value proposition. The table below shows this theoretical relationship:
Deviation of orthogonal solar beam (degree) | Relative output w.r.t. orthogonal beam (%) |
---|---|
0.0 | 100.0 |
0.1 | 100.0 |
1.0 | 99.98 |
2.5 | 99.90 |
5.0 | 99.62 |
10.0 | 98.48 |
20.0 | 93.97 |
Concentrated Solar Trackers
Concentrated PV solar trackers require by nature quite different tracking accuracies. First, the receivers typically have an acceptance angle of much less than +/- 1.0 degree. Even within the acceptance angle, there is usually some degradation as the solar beam deviation approaches the limits of the acceptance angle. As a result, CPV solar trackers typically have extremely high electro-mechanical design standards. Similarly, encoder and/or inclinometer feedback is typically not sufficient to guarantee optimum positioning.
Movement Frequency
During the winter at noon time at middle latitudes the apparent motion of the Sun can be on the order of 2 to 3 degrees every ten minutes, while during the summer, the movement can be as great as 10 degrees. For PV based trackers, it is generally a good idea to minimize motor starts and stops to promote longevity of the electro-mechanical systems. Such algorithms will consider both a movement time interval and minimum angular adjustment.
Production Gain from Trackers
The energy gain of PV systems based on trackers versus stationary is dependent on location and season. Estimates and actual measurements indicate, on an annual basis, single axis trackers gain ~20% additional power compared to a fixed angle system, while dual axis tracker systems can gain ~40%. Single axis trackers typically follow the sun by elevating the modules around a North-South axis, while dual axis trackers typically rotate panels around the horizontal axis and adjust for elevation in the vertical axis.